The Cost of a Product Recall
A food product recall can be an extremely costly process, and the continuation of food processing, whilst managing a recall, can be a significant challenge. But if you get pests into your food preparation or management chain, this is a necessity to limit the spread of disease and manage an infestation.
So, why then, are there thousands of food management companies and food preparation supply chains that don’t employ pest control companies?
Why Does Product Recall Occur?
In the UK, in 2016, 80 items of food were issued with a product recall notice, an immediate notification issued by the supplier or processor about a potential harmful defect with the product. This was up 29% from the previous year. In 2018, this number decreased to 78, which is still far too high.
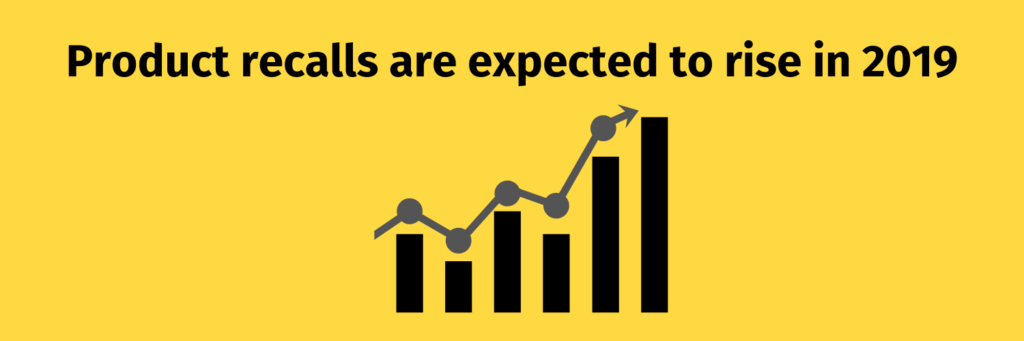
One of the leading causes of product recalls last year were the traces of Salmonella, E Coli and other contaminants like Listeria monocytogenes in the product. A recall is usually issued by the Food Standards Agency (FSA) after either being notified by the production company, or during product tests by their own inspectors.
Product recalls are seriously damaging for brands and are usually issued if the FSA finds the products to be ‘seriously damaging to human health’ or are ‘likely to cause health concerns’.
The Direct Cost of Product Recall
There are many costs associated directly with a product recall, which can quickly turn a profit-taking food business, into a loss-making company. Whilst there are a lot of costs that are directly associated with a product recall, it’s reported that many recalls can affect a business’ bottom line for many years after. The direct costs are fairly expensive too and include.
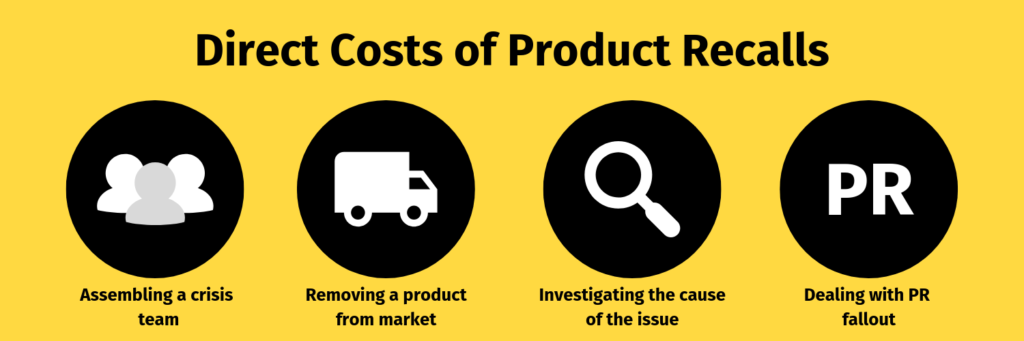
Assembling a Crisis Team
The first step is assembling a team that is able to directly deal with the recall; identifying products, handling returns and removing the initial issue. This will require a fairly significant team depending on the scale of the business, the more products distributed, the larger the team will need to be.
Removing the Product from Market
This is a logistical nightmare for food processing businesses. It requires clear communication with wholesalers, suppliers and stores in order to fully take the product off the market. This in itself is a challenge, but the significance and urgency are greatly increased if these products are already distributed to customers. They will need to be notified immediately of any danger. Not doing so could cause significant PR fallout and legal issues.
Investigating and Addressing the Cause
The most important part of the process is addressing the reason the recall had to take place in the beginning. Whether this is a complete overhaul of the processes involved in the food processing, or alternatively, an investigation into certain methods of process or creation. Identifying these issues and finding a strategy to stop them from happening is essential to re-opening a fully functional food-processing plant.
Dealing with the PR fallout
If you managed to find the issue quickly enough, the recall won’t stir up much attention. If a public recall needs to be issued, this is where things get complicated. It may require specialist PR advisors to limit the fallout regarding the recall.
Bacteria Infected Food
With more than 70% of product recalls in the food industry down to bacteria or contamination in food, you’d think that food processing or baking companies would take a proactive approach to ensure that those contaminants do not get into the food.
However, with pests and insects being a main cause of contamination, reports suggest that only 66% of food businesses in the UK are taking a proactive approach when it comes to ensuring the food processing areas are clean and pest-free, as opposed to more than 85% in the U.S.
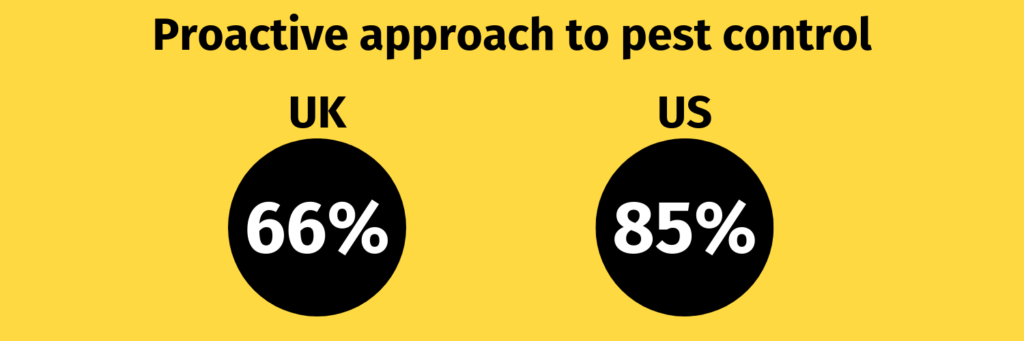
In fact, in the UK alone, more than 55% of food processing businesses reported to the Centre for Economics and Business Research that in the last year they have lost at least one day due to infestation.
What Pests Cause Product Recalls
There are many pests that are likely to cause an infestation in the food processing industry. However, some are more likely to cause contamination than others. The ones that food businesses need to be wary of are as follows:
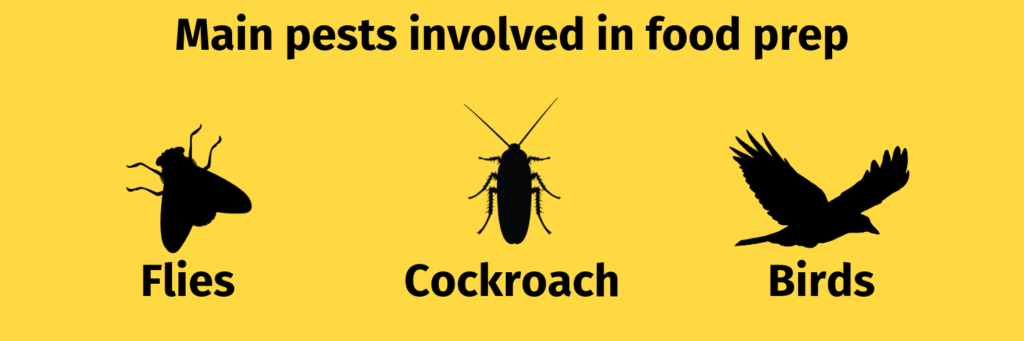
Flies
Flies are common pests in the food processing industry and are a common factor in the spread of E.Coli. Where there is food, you can expect flies to follow. And with flies come harmful diseases which are picked up from animal faeces and already contaminated food elsewhere. This can pose a significant risk to the hygiene of a food processing business.
Cockroaches
Whilst less common in the UK, there are some conditions which allow cockroaches to breed, and continue to thrive. Unfortunately, these conditions are likely to be in food processing areas. Cockroaches feed on any human food and can easily spread Salmonella through depositing faeces or vomit on food.
Birds
Research suggests that birds can carry more than 50 kinds of disease. Some of those can be incredibly dangerous for human consumption, even leading to severe illness and death. Birds are commonly found in the rafters of factories and food processing plants, which can cause them to easily pass parasites and deposit faeces in the factory.
How Can you Stop Pests Causing Product Recalls?
For many domestic pest issues, a reactive pest control method is usually recommended. Only acting once an infestation has been identified and a clear plan is in place. However, when it comes to domestic pest control, a proactive approach is significantly better for several reasons.
Pests in commercial plants are incredibly detrimental to the hygiene of public produce. For this reason, it’s recommended that a pest control contract is a better option. This allows pest control providers to survey the factory on a monthly basis and ensure there are no pests and there is no way for pests to enter.
This helps ensure a level of hygiene is maintained and any issues with possible infestations are identified quickly. Thankfully, here at Confirm A Kill, we understand that product recalls are your worst nightmare and offer pest control contracts to suit your business, you can view more here.